Apple is best known for its futuristic, spaceship-like headquarters in Cupertino, California.
But what many people don’t know is that the tech giant also has a huge campus in Ireland.
Apple’s Cork campus opened its doors in 1980 with a single manufacturing facility and just 60 employees.
Fast-forward to today, the site is home to more than 6,000 employees, and serves as Apple’s European headquarters.
The tech giant is usually extremely private about what happens behind closed doors.
However, MailOnline’s Science and Technology Editor, Shivali Best, was invited to Cork for a rare look inside the testing labs.
There, Apple puts its top-secret prototypes through their paces – and the gadgets won’t leave until they pass the rigorous tests.
From bashing and prodding, roasting and freezing, here’s what really goes on inside Apple’s European testing labs.
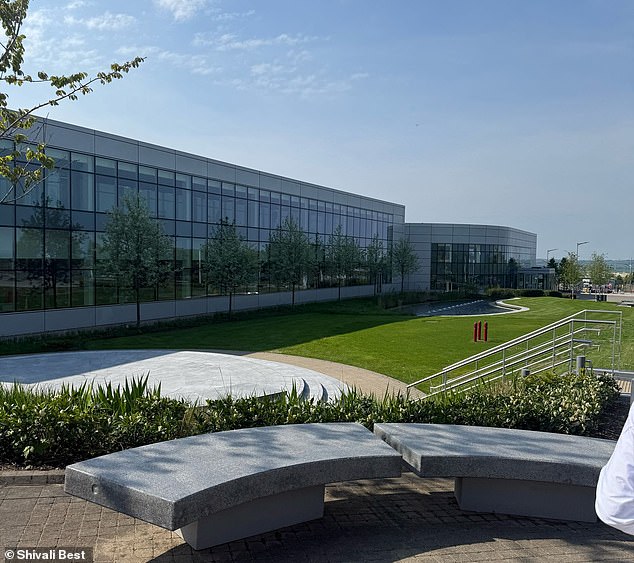
Apple is best known for its futuristic, spaceship-like headquarters in Cupertino, California. But what many people don’t know is that the tech giant also has a huge campus in Ireland
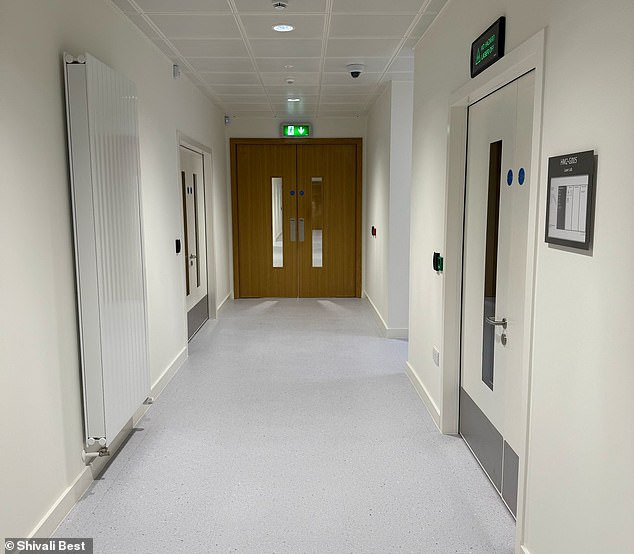
Chaperoned by several eagle-eyed Apple employees, we made our way down a series of white corridors, which wouldn’t have looked out of place in the latest series of Severance
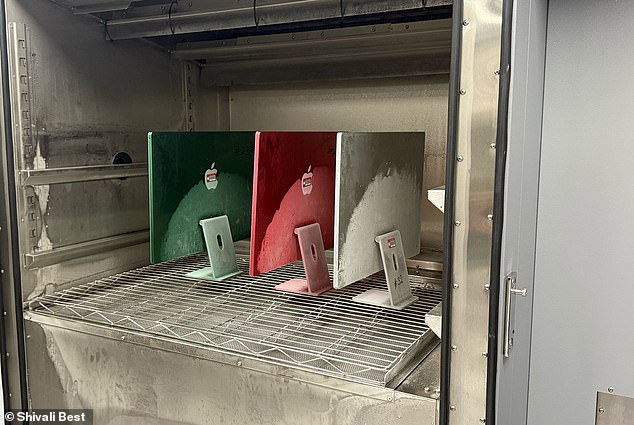
The iMacs are subject to a cold chamber, where they’re blasted with short gusts of -20°C air, interspersed with heat
Set against the stunning Irish landscape, Apple’s Cork campus is mostly made up of a series of glass buildings, interspersed with slick landscaping.
To our surprise, however, we were escorted just off the main campus, to an unsuspecting stone building.
Chaperoned by several eagle-eyed Apple employees, we made our way down a series of white corridors, which wouldn’t have looked out of place in the latest series of Severance.
Passing rooms discreetly labelled things like ‘Laser Lab’, and ‘Water Services’, we eventually reached our destination – the Reliability Testing Lab.
There, we were walked through the series of meticulous tests that each new iPhone, MacBook, and iPad must endure.
Speaking to MailOnline, Tom Marieb, Apple’s Vice President of Product Integrity for Hardware Engineering, explained: ‘We do a huge variety of tests. Our main goal is to meet customers where they actually live and are.
‘A lot of our tests aren’t “standard tests” – they’re tests that we’ve developed over time to mimic real life and usage.’
First up is a huge oven, where we find four iMacs (with a combined cost of over £5,000!) being blasted with 65°C temperatures and high humidity.
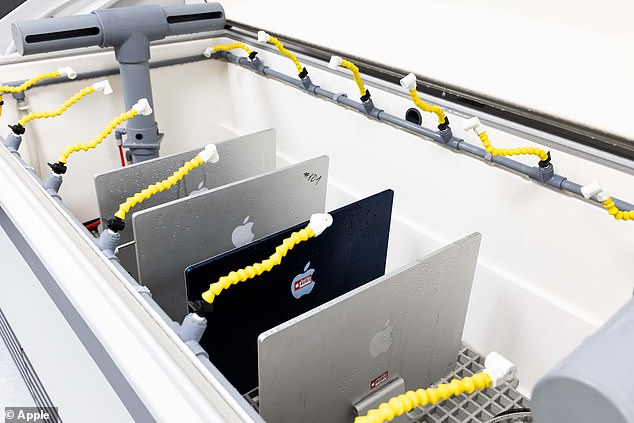
The ‘salt test’ see the devices sprayed with salt water to recreate the conditions using a gadget on the beach
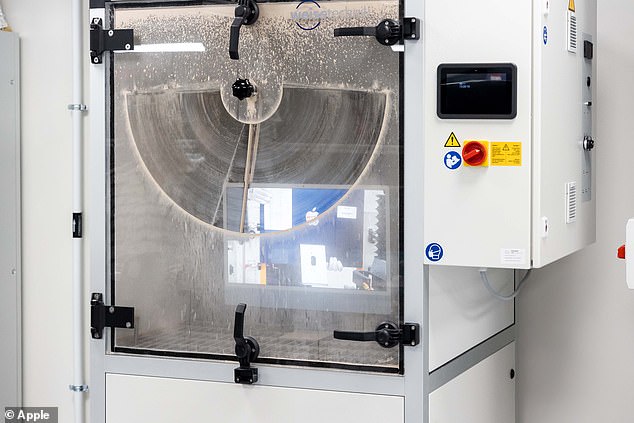
Using the finest dust available, Apple blasts its devices to see if their ports can withstand the bombardment
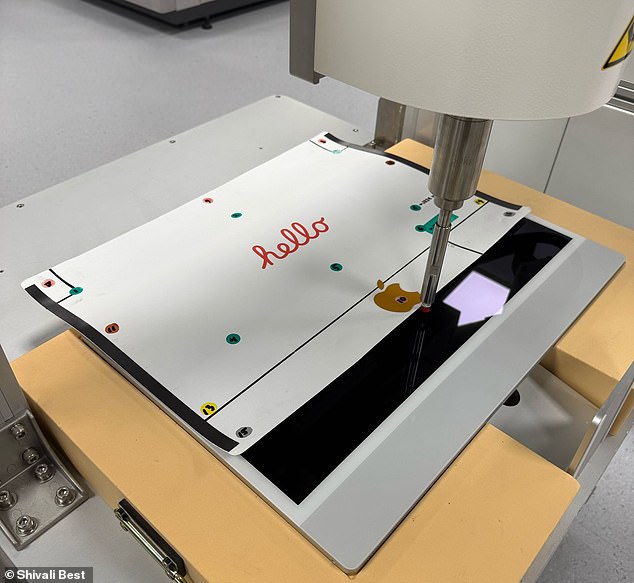
Other tests in this lab are slightly less dramatic – but are no doubt just as important
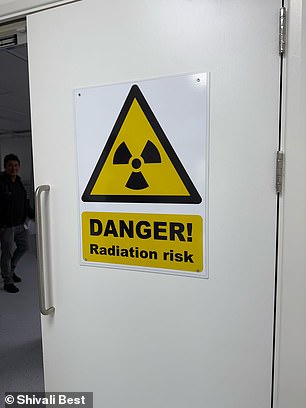
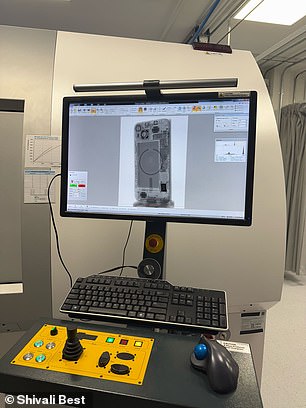
If the problem is internal, it’s over to the Radiation Lab for a closer inspection. Labelled with huge signs reading ‘DANGER! Radiation risk’, this lab is kitted out with the latest, state-of-the-art machines, which allow Apple’s technicians to peers inside at almost every level
This, Apple tells us, is to test both the internal and external elements – and if any fail, it’s back to the drawing board.
Next is the shipping and transportation test, which involves vibrating and dropping a device – on its own, in a box, and in a pallet.
‘If you look at the industry standard, they’d drop it on a piece of steel,’ Mr Marieb explained to MailOnline.
‘Well, to us that’s not interesting. You don’t live in a house with steel floors.
‘So we look at wood, we look at granite, we look at asphalt – real surfaces that people really use.’
For the next test, dubbed the ‘tip test’, I was even invited to get involved.
Donning a pair of gloves, I tentatively toppled a £1,299 iMac over onto a hard surface – something I’ll probably be having nightmares about for the next few weeks.
Thankfully, the pricey gadget survived the test, and it was on to the next chamber – the dust test.
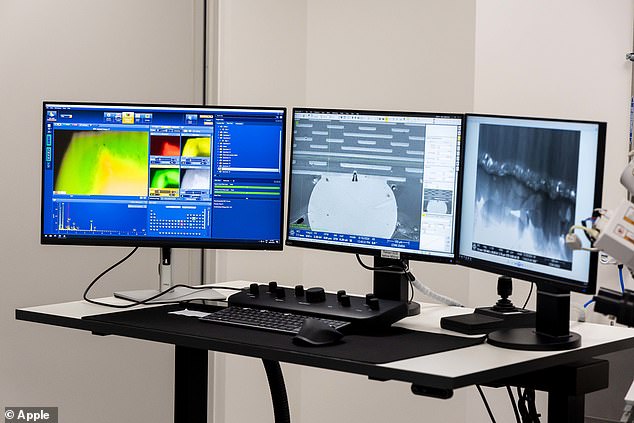
Apple has invested in a scanning electron microscope and a focused ion beam (FIB) microscope, which can achieve imaging resolution of just 5nm
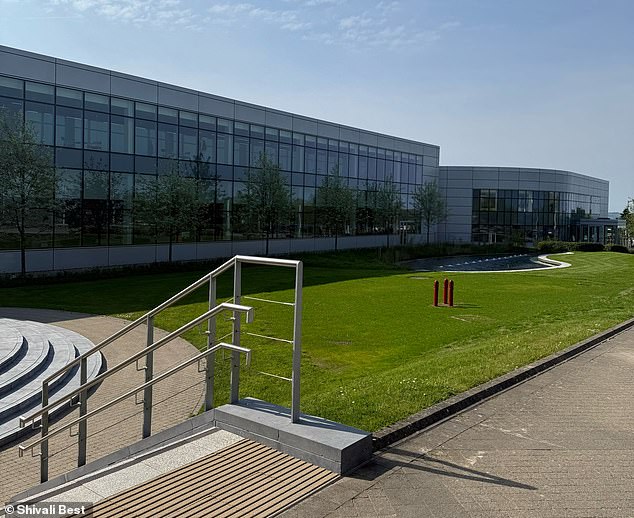
Set against the stunning Irish landscape, Apple’s Cork campus is mostly made up of a series of glass buildings, interspersed with slick landscaping
Using the finest dust available, Apple blasts its devices to see if their ports can withstand the bombardment.
‘We aim to mimic the Arizona desert in that test. So we purposefully find exactly the composition of the sand,’ Mr Meriab explained.
Now, having survived the heat test, the iMacs are subject to a cold chamber, where they’re hit with short gusts of -20°C air, interspersed with heat.
This, an Apple employee tells us, is to mimic the experience of a device being placed in the hold of an airplane, before being used in a sunny country.
In addition, the ‘salt test’ see the devices sprayed with salt water to recreate the conditions using a gadget on the beach.
Other tests in this lab are slightly less dramatic – but are no doubt just as important.
One machine’s entire job is to test a cable being pulled in and out of the charging port, while another simply presses the power plug from different angles.
Meanwhile, one robot mimics sweaty fingers by repeatedly touching the screen with an infused cloth.
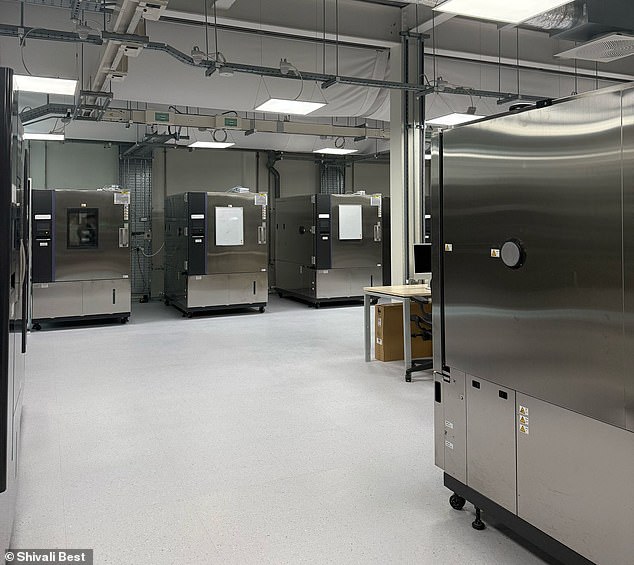
While this level of testing might sound excessive, it’s all part of Apple’s ‘longevity by design’ approach
‘Our goal is to find reality and then make it synthetic in a repeatable way to do science on it,’ Mr Meriab added.
‘So that covers a huge gamut of different things. Wherever you might dream of taking it, we’ve thought of it and tested it.’
If Apple detects any external problems in the reliability tests, the entire design might need to be reconsidered.
But if the problem is internal, it’s over to the Radiation Lab for a closer inspection.
Labelled with huge signs reading ‘DANGER! Radiation risk’, this lab is kitted out with the latest, state-of-the-art machines, which allow Apple’s technicians to peers inside at almost every level.
At the most basic level is an X-ray machine, which brings up a 2D scan almost instantly – much like an X-ray machine would let you examine a broken limb in a hospital.
If the technicians need a 3D scan, it’s over to the CT machine, which creates a 360-degree view of the device.
But the machines don’t stop there.
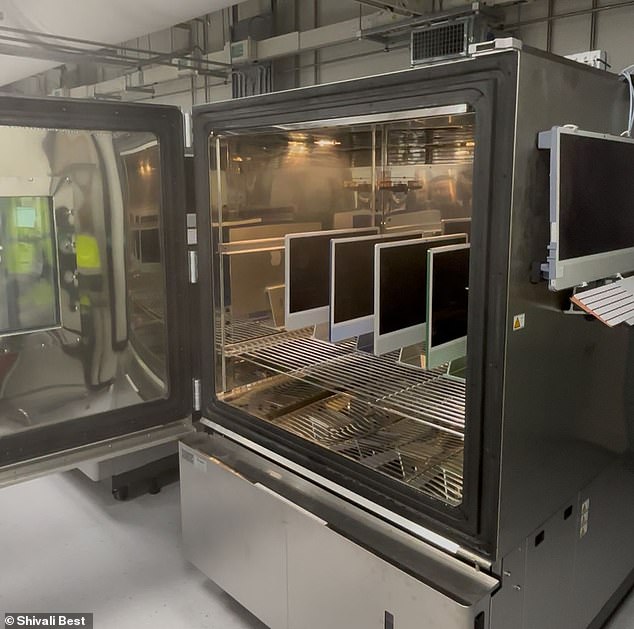
First up is a huge oven, where we find four iMacs (with a combined cost of over £5,000!) being blasted with 65°C temperatures and high humidity
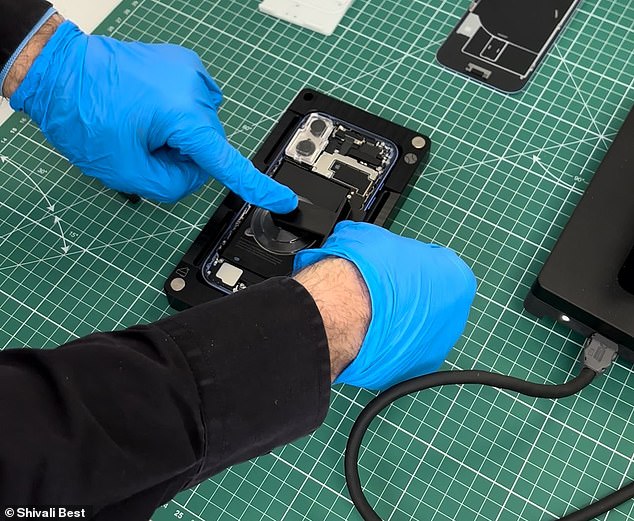
According to the tech giant, there are now hundreds of millions of iPhone that have been in use for more than five years – and that number is growing
Apple has also invested in a scanning electron microscope and a focused ion beam (FIB) microscope, which can achieve imaging resolution of just 5nm.
Given the tiny size of some components, this allows the technicians to pinpoint exactly what might be wrong with a device – and how to fix it.
While this level of testing might sound excessive, it’s all part of Apple’s ‘longevity by design’ approach.
This company-wide effort aims to increase product longevity through new design and manufacturing technologies, ongoing software support, and expanded access to repair services.
According to the tech giant, there are now hundreds of millions of iPhone that have been in use for more than five years – and that number is growing.
‘We design these things to last a long time – that’s our goal,’ Mr Meriab added.
‘If somebody wants a phone at a more frequent level, that’s hopefully because we’ve made new features that are compelling.’